Last updated on June 8th, 2025 at 02:31 pm
Wheeled off-road machines require efficient and precise steering systems to navigate challenging terrains and perform specific tasks effectively.
Different types of steering systems are used in mobile equipment, each designed to optimize control, maneuverability, and stability. This article provides a detailed look into the four major steering systems found in off-road wheeled machinery:
- Dual-Path Hydrostatic Transmission
- Ackerman Steering
- Articulation Steering
- Combination Steering
Understanding how these systems work and their applications in different types of equipment can help operators, engineers, and enthusiasts appreciate their role in vehicle performance.
Dual-Path Hydrostatic Transmission Steering
A dual-path hydrostatic transmission (HST) consists of two independent hydrostatic transmissions that work together to provide both propulsion and steering.
Working
Dual-path hydrostatic transmission systems use hydraulic flow to control wheel speed. One hydraulic pump and motor control the right-side drive, while another set powers the left-side drive. This setup allows the machine to change direction by adjusting the speed of each side independently. When a turn is initiated, the hydraulic control system slows down the inside wheel while increasing the speed of the outside wheel, effectively creating a turning motion.
Applications
- Skid steers
- Self-propelled windrowers
- Zero-turn-radius (ZTR) lawnmowers
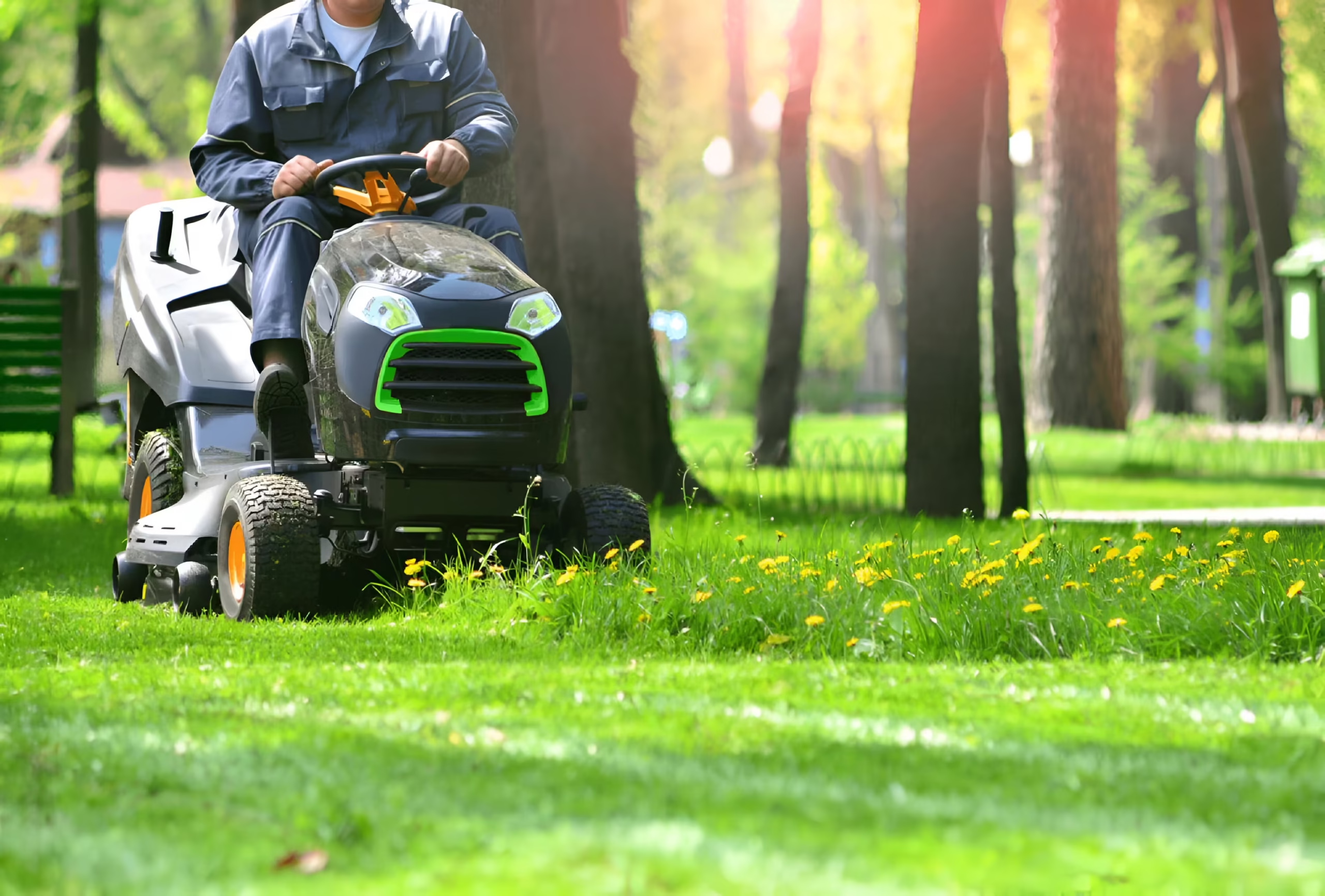
Zero-turn lawn mowers use a dual-path hydrostatic transmission for precise steering and maneuverability.
Advantages
- Zero-turn capability – Essential for machines that require high maneuverability in confined spaces.
- Smooth, continuous steering – No mechanical linkages mean fewer parts to wear out and smoother operation.
- Independent wheel control – Allows greater flexibility in navigating rough or uneven terrain.
- Reduced operator fatigue – Easier to control compared to mechanical systems.
Challenges and Limitations
- Higher complexity – Requires skilled maintenance due to the intricate hydraulic components.
- Potential power loss – Efficiency can be affected if hydraulic fluid becomes contaminated or if leaks occur.
- Increased cost – More expensive than mechanical steering systems due to hydraulic components.
Ackerman Steering
Ackerman steering, named after Rudolf Ackerman, is designed to improve turning efficiency. It ensures the inside wheel turns at a sharper angle than the outside wheel, allowing both wheels to follow their natural turning arcs. Without this geometry, vehicles would struggle to make smooth turns.
Working
The Ackerman steering mechanism ensures that the inner wheel turns at a greater angle than the outer wheel. This difference in angle aligns the wheels’ paths with their respective turning radii, preventing tire drag and allowing smooth cornering.
Power-Assist Steering
Power-assist steering uses hydraulic pressure to help the operator steer heavy loads. It reduces the effort needed to turn the wheels, making steering more efficient. There are two main types:
Integral Power Steering Gear
This system consists of:
- Adjusting Screw
- Unloading Valve
- Worm
- Torsion Bar
- Rotary Valve
- Input Shaft
- Piston Rack
- Output Shaft
- Housing
- Balls
- Valve Housing
ZF Aftermarket has provided very detailed information about Integral Power Steering Gear. When the driver turns the steering wheel, the internal shaft rotates, engaging the rotary valve. The valve directs hydraulic fluid to the power piston, which moves and meshes with the sector gear, assisting in steering.
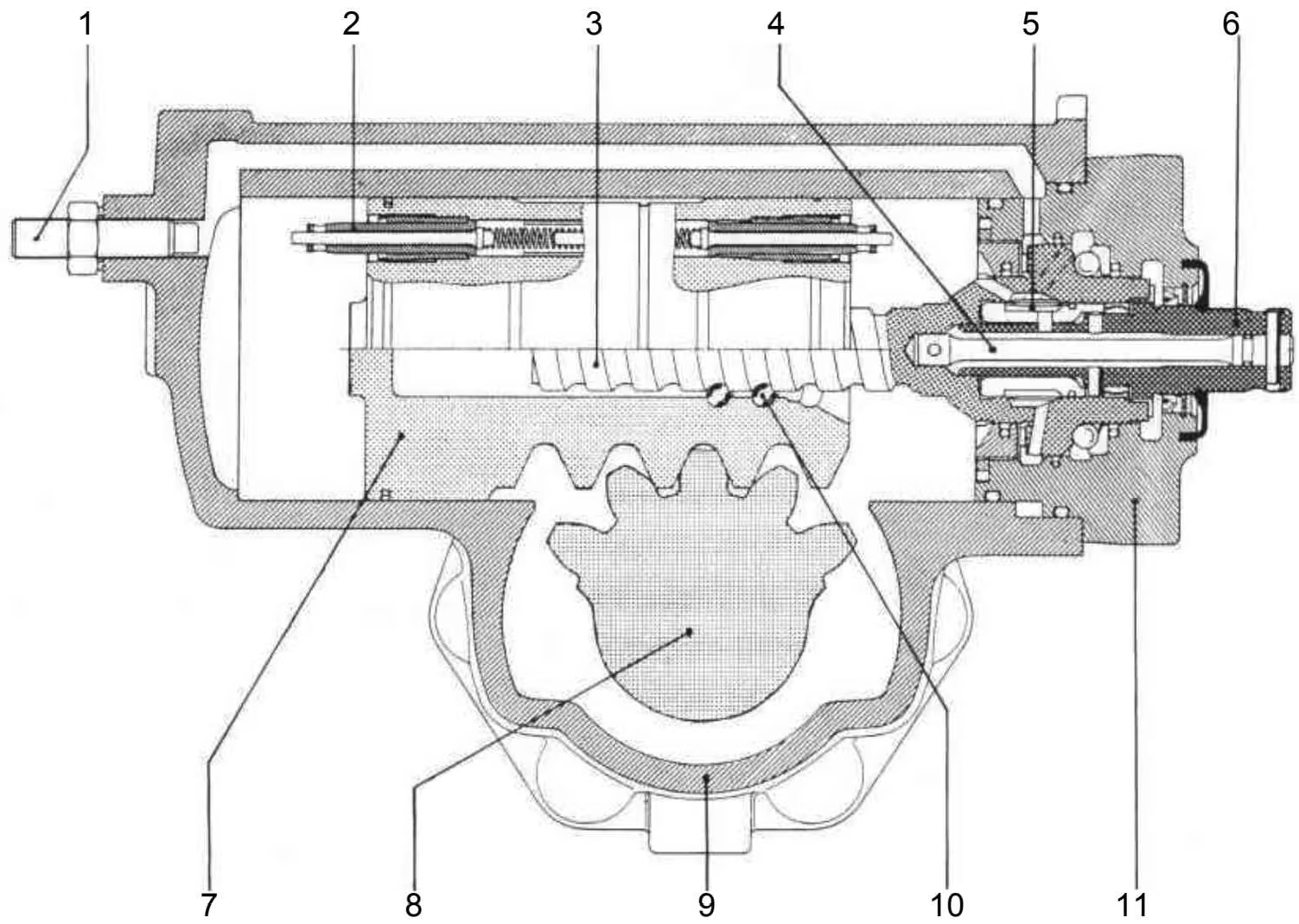
An integral power steering gear uses hydraulic pressure to assist in steering, reducing operator effort in heavy machinery.
Power Rack-and-Pinion Steering
Similar to manual rack-and-pinion steering but with hydraulic assistance, this system uses a control valve to direct fluid to either side of the rack’s power piston. The hydraulic pressure helps move the rack, reducing steering effort.
Note: Power rack-and-pinion steering is uncommon in mobile machinery and is rarely used in large on-highway trucks.
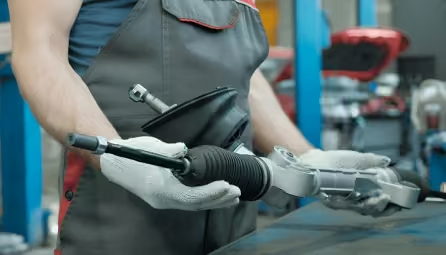
Steering Rack
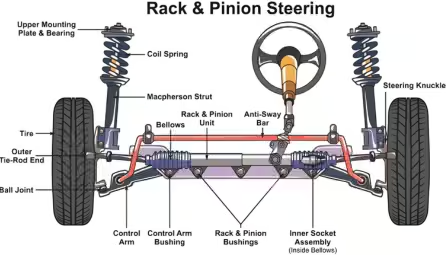
Rack & Pinion Steering
Applications
- Passenger cars and trucks
- Forklifts and industrial vehicles
- Off-road machinery
Advantages
- Reduces tire wear – Proper alignment prevents excessive friction between tires and the ground.
- Improves maneuverability – Essential for making smooth and controlled turns.
- Enhances vehicle stability – Ensures that all wheels contribute effectively to turning motion.
- Increases fuel efficiency – Reduces resistance, leading to better energy conservation.
Challenges
- Limited application in heavy-duty vehicles – Not ideal for extremely large or articulated machines.
- Requires precise alignment – Small misalignments can lead to uneven tire wear and steering inefficiencies.
- Less effective on rough terrain – Not suitable for extreme off-road conditions where articulation is required.
Articulation Steering
Working
Articulation steering is commonly used in large off-highway machines. The system consists of an articulation joint that connects the machine’s front and rear frames. Hydraulic cylinders pivot the frames, steering the machine left or right.
Applications
- Agricultural four-wheel-drive tractors
- Articulated dump trucks (ADTs)
- Scrapers and motor graders
- Large compactors, trenchers, and wheel loaders
- Pivot-steer telehandlers
Advantages
- Improved maneuverability – Reduces turning radius, making it easier to navigate tight spaces.
- Better weight distribution – Helps maintain traction and balance on uneven terrain.
- Durability – Less wear on components compared to traditional steering linkages.
- Enhanced operator visibility – Provides a better field of view when navigating obstacles.
Challenges
- More complex maintenance – Hydraulic components require regular upkeep.
- Higher cost – More expensive to manufacture and repair compared to standard steering systems.
- Potential instability at high speeds – Articulated vehicles can be harder to control at higher velocities.
Combination Steering
Some off-road machines use combination steering, which combines:
- Articulation steering with Ackerman front-steering
- Two articulation joints for greagter flexibility
Applications
Motor Grader Steering
Motor graders offer dual steering control:
- Articulation joint steering (provides 20° or more of rotation)
- Front axle steering
Operators can steer both systems together or independently:
- Same direction: Helps make sharp 180° turns in tight spaces.
- Opposite directions: Keeps the front axle away from windrows while the rear frame stays aligned behind the blade. This helps avoid obstacles while grading.
Case IH 4WD Tractor Steering (AccuSteer)
Case IH Steiger 4WD tractors use combination steering, which includes:
- Articulation-only mode (traditional center pivot): The 9310, 9330, and STX AccuSteer models have two articulation points—one at the center and one at the front axle.
- Combination mode (front axle articulates first, followed by the rear): In combination mode, the front articulation moves 10° first, then the rear adds 42°, totaling 52° of articulation.
Multi-Axle Steering
Some machines use multiple steerable axles beyond the traditional four-wheel steering. Examples include:
- All-terrain cranes (up to 4 steerable axles)
- Concrete pumper trucks
- Aviation rescue fire-fighting (ARFF) trucks
- Military vehicles (some with 8 steerable axles)
Multi-axle steering reduces tire wear, improves maneuverability, and allows crab steering (moving diagonally). Some cranes, like Grove all-terrain cranes, use steer-by-wire technology for precision control.

Multi-terrain crane with seven axles, including front and two rear steer axles.
Advantages
- Increases maneuverability – Allows complex machines to operate in confined spaces.
- Enhances control in tough terrains – Useful in farming, construction, and emergency response vehicles.
- Optimizes tire wear and fuel efficiency – More efficient steering reduces stress on components.
Challenges
- Higher mechanical complexity – Requires advanced engineering and maintenance.
- Training required for operators – More complicated than single-mode steering systems.
Conclusion
Each steering system in off-road machinery serves a distinct purpose, balancing maneuverability, control, and stability. Dual-path hydrostatic transmission enables zero-turn capability, ideal for compact machines. Ackerman steering improves turning efficiency and stability but suits lighter-duty vehicles. Articulation steering excels in large off-highway equipment, while combination steering merges multiple systems for precision.
The right choice depends on operational needs—tight spaces favor hydrostatic or articulation steering, while road performance benefits from Ackerman. For heavy-duty applications, combination and multi-axle steering offer superior control. Understanding these systems ensures optimal performance in challenging terrains.
What’s Next?
So far in our steering series, we have covered:
Post 1: The applications of steering units, along with a deep dive into their components (spool, sleeve, centering pin, etc.) and design elements (various valves like inlet check, port relief, and load-sensing relief valves).
Post 2: A breakdown of different types of steering units, including open center, power beyond, and closed center steering units. We also explored load sensing circuits and their static/dynamic signal systems.
Post 3: Analyzed steering work circuits, covering reaction vs. non-reaction steering. We also discussed advanced features like 2-speed technology, Q-Amp flow amplification, wide angle steering, and cylinder dampening—along with their applications.
Post 4: A Detailed focus on the steering control unit’s spool-sleeve mechanism. Steering unit operates in different modes, including 4-wheel steer, crab mode, and 2-wheel steer mode.
Post 5: In this post, we explored hydraulic steering amplifiers—why they are needed, their working principles, key components, and calculation. These amplifiers significantly improve steering response in large off-road machines by boosting hydraulic flow beyond what a Steering Control Unit (SCU) alone can provide.
🚀 Coming Up Next (Post 7):
Now that we’ve explored different types of steering, it’s time to get into the numbers. In the next post, we’ll cover essential calculations like steering angle, turning radius, and hydraulic flow to understand how each system performs.
If you enjoyed this post, I’d really appreciate it if you could subscribe. I’m 100% planning to dive deep into hydraulics and break it down into simple terms for you!