Last updated on June 8th, 2025 at 02:31 pm
Heavy equipment like excavators often need different attachments for different jobs. For example, you might need to switch from a large bucket to a smaller one, or from a bucket to a breaker or grapple. These changes happen many times during a normal workday. However, switching attachments can take a lot of time, which reduces the machine’s productivity.
To solve this problem, quick hitch coupler are used on excavators. They allow operators to change attachments much faster, saving time and increasing productivity.
A quick hitch is a tool that makes it easier and faster to attach and remove different tools (like buckets, grapples, or rock breakers) to heavy machines like excavators. It attaches to the end of the excavator’s arm and allows the operator to quickly switch between different attachments without needing much effort.
Without a quick hitch, you would need to connect and disconnect attachments using pivot pins. This method can be a hassle because:
- It takes a lot of time to change attachments.
- Multiple changes might be needed throughout the day.
- The pins can get rusty and stuck, making them hard to remove.
- Larger pins can be heavy and tough to handle by hand.
Quick hitches solve these problems by making the process quicker, easier, and more efficient.
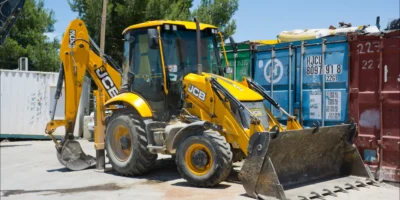
Types of Quick Hitch
Quick hitch couplers are essential tools in hydraulic and construction equipment, providing fast and secure attachment changes. There are two main types:
- Dedicated Quick Hitch: Designed for specific attachments, this system maintains optimal geometry between the attachment and the machine’s dipper arm, preserving breakout force and bucket tip radius. However, it restricts the machine to only compatible attachments, requiring significant investment in dedicated equipment.
- Pin System Quick Hitch: The most versatile option, this quick hitch connects via two pins on standard attachments, making it compatible with various tools. While it adds some length to the dipper arm and slightly reduces breakout force, its adaptability makes it popular in construction.
Pin system quick hitches come in three varieties:
- Manual: Requires manual locking.
- Semi-Automatic: Partially automated locking.
- Fully-Automatic: Fully locks and secures the attachment without manual input.
Each quick hitch uses a locking mechanism and safety device (like a pin or latch) to ensure the attachment remains securely connected to the equipment, preventing accidental disconnections.
Manual Quick Hitch System
A manual quick hitch system is designed to securely connect attachments to heavy equipment using a simple mechanical process.
Once the attachment is engaged, it is held in place by a manual locking mechanism, which could be a screw-operated latch, controlled with a ratchet, or a sprung latch, operated by a detachable lever known as a ‘tommy-bar.’
To ensure safety, a manual safety pin is inserted after the latch is engaged. This prevents the latch from accidentally opening, which could cause the attachment to disconnect unexpectedly. While the manual quick hitch system requires more effort to operate compared to automatic systems, it remains a reliable and cost-effective solution for many construction and hydraulic applications.
This system is commonly used in heavy equipment such as excavators, backhoe loader, where changing attachments manually is still preferred for its simplicity and durability.
Semi Automatic Quick Hitch
A semi-automatic coupler requires a safety pin to be manually inserted after attaching the equipment. However, the coupler can still function without the safety pin, which is never recommended and is highly unsafe.
This is why semi-automatic couplers are typically banned in most workplaces.
While the machine attachment is secured by a hydraulically operated latch, the safety pin provides additional security and must be fitted manually.
As demonstrated in the video, during disassembly, the safety pin was removed, but it was not reinstalled after reassembly, creating a dangerous situation. Unfortunately, many operators neglect to install the safety pin, which significantly increases the risk of accidents.
To eliminate this risk, fully automatic quick hitches are now widely used, as they remove the need for manual safety pin installation.
Fully Automatic Quick Hitch
The fully-automatic quick hitch system provides a seamless and safe attachment process for heavy equipment, all controlled from within the machine cab.
It secures the attachment using a hydraulically operated latch and automatically engages a safety device. This safety device may include a hydraulic check valve or a spring mechanism to prevent accidental release of the latch.
Unlike manual or semi-automatic systems that require manual safety checks outside the cab, the fully-automatic system ensures both the latch and safety mechanisms are engaged hydraulically, reducing the need for human intervention.
This makes it a highly efficient and safe option, particularly in construction and hydraulic applications where time and safety are critical.
Quick Hitch Operation
Ensuring correct operation of the hitch at all times avoids premature wear of the hitch.
Mounting Quick Hitch to Excavator
Mounting Attachment to Quick Hitch
Quick Hitch Coupler in Disengaged View
To install the attachment using the quick hitch coupler, first engage the latch side pin.
(Blue circles indicate the attachment pins)
Quick Hitch Coupler in Engaged View
Position the quick hitch so that the sliding hook connects with the other pin on the attachment, aided by the extending hydraulic cylinder.
This action locks the attachment securely in place, making it ready for use.
(Blue circles indicate the attachment pins)
Quick Hitch Guideline:
To ensure safety for all, the following guidelines must be strictly adhered to:
- Cylinder Pressure: Maintain a minimum pressure of 200bar on the cylinders.
- Hoses: Use double-braided hoses rated for 350bar with a safety factor of 3.
- Hydraulic Oil: Ensure that only hydraulic oil compatible with the machine’s hydraulic system is used.
- Switch Placement: Install the control switch in a secure position within the cab to prevent accidental activation. It should be placed just outside the operator’s main comfort zone, yet remain easily accessible, allowing operation without losing visual contact with the quick hitch. Use a toggle switch with an aircraft-style safety cover.
- Switch Labelling: Label the switch clearly to prevent accidental disengagement of the hitch.
- Audible Alerts: The switch must trigger a buzzer when in the off position. Additionally, an alarm must sound whenever the machine is in a mode that enables control for engaging or disengaging attachments. The machine must not be used without this functionality.
- Hydraulic Control Valve: Use an on/off valve without a neutral position to ensure full pressure to the cylinder.
- Low-Pressure Alarm: A low-pressure alarm must be installed in the cab to alert the operator to any pressure loss that could compromise the primary retention system of the quick hitch (hydraulic cylinder). The quick hitch must not be operated while the low-pressure alarm is active.
Quick Hitch Suppliers:
Quick hitches are typically produced by independent manufacturers rather than the original equipment makers of the machines. A list of quickhitch
manufacturers is provided for informational purposes.
EpicHydraulic does not endorse or specifically recommend any products or services.
Conclusion
In summary, quick hitch couplers make working with excavators much more efficient and safe by allowing operators to quickly switch attachments. Without them, changing attachments can be a slow, labor-intensive process that involves handling heavy, sometimes stuck, pins. Quick hitches streamline this by offering various levels of automation—from manual to fully automatic—each suited to different needs. Fully automatic systems, in particular, stand out for their convenience and enhanced safety, as they remove the need for manual checks. Following proper safety and operational guidelines is crucial to ensure these tools work reliably and safely on the job.
If you enjoyed this post, I’d really appreciate it if you could subscribe. I’m 100% planning to dive deep into hydraulics and break it down into simple terms for you!