Last updated on June 8th, 2025 at 02:31 pm
A hydraulic rock breaker (hammer) is a type of construction machinery that is mounted on excavators, backhoes, skid steers, mini-excavators, and stationary plants.
Driven by hydraulic power it breaks rocks into smaller sizes or demolishes concrete structures into manageable pieces.
History of Rock Breaker
The evolution of rock breakers began in 1963 when Krupp secured the patent for the first manufactured hydraulic hammer and by 1967, the Krupp HM 400 was introduced. Later, in 2002, Atlas Copco acquired Krupp Berco Bautechnik, further advancing the industry.
(Read Acquisition Article)
Meanwhile, in 1965, Montabert made history by developing the first-ever handheld hydraulic jackhammer. This shift from pneumatic to hydraulic technology paved the way for significant advancements. By 1969, Montabert introduced the BRH500, the first hydraulic rock breaker designed for excavators, marking the beginning of a highly successful hydraulic breaker product line.
Applications of Hydraulic Hammers
Hydraulic hammers, also known as rock breakers, are versatile tools used in various heavy-duty tasks. Hydraulic hammers can be fitted with different tools—such as chisels, tamping blocks, conical picks, and wedges—allowing them to perform multiple tasks efficiently. Their applications include:
- Rock excavation: Breaking and developing rock formations.
- Demolition: Dismantling reinforced concrete structures and buildings.
- Frozen soil breaking: Splitting frozen ground for pile driving.
- Roadwork: Breaking up asphalt roads and road surfaces.
- Utility access: Opening underground utility systems.
- Soil compaction: Compacting soil for construction.
- Excavation: Digging pits and trenches.
- Pipeline installation: Laying main pipelines.
- Fence removal: Breaking and dismantling fences.
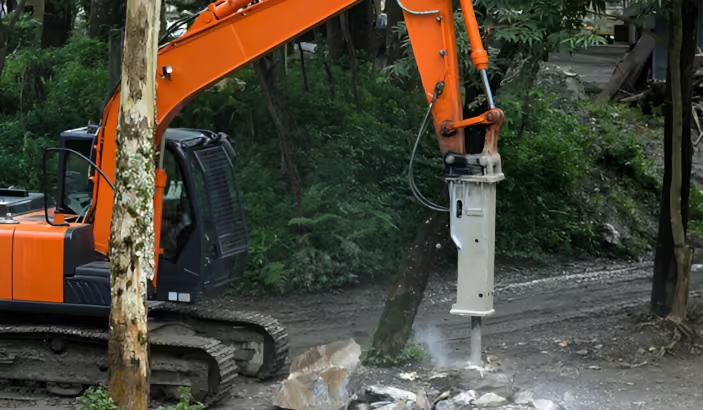
Rock Breaker breaking up road surfaces.
Components of a Hydraulic Hammer
The design of a hydraulic hammer varies, but it generally consists of two main sections:
- Control Unit: Regulates hydraulic flow and pressure.
- Impact System: Converts hydraulic energy into powerful blows.
Some hydraulic hammers use tie bolts for housing assembly, similar to tie-rod cylinders (also known as through bolts). Others feature an integral design without tie bolts. In hammers with tie bolts, an internally broken bolt can disrupt operation, preventing the hammer from functioning properly.
Key components of the impact system include:
- Frame (body): Houses and supports internal components.
- Guide sleeves: Direct the movement of the striking pin and working tool.
- Tug and distributor: Control hydraulic flow for precise operation.
- Piston: Positioned in the middle of the striker, delivering high-impact force.
- Breaker tool (chisel tool): The working end that contacts and breaks the material.
- Nitrogen chamber: Stores energy to enhance striking power.
- Pressure and drain lines: Supply hydraulic fluid to the piston for smooth operation.
Some nitrogen-assisted hammers, such as those from Caterpillar, also include an accumulator to further improve performance. These components work together to generate powerful, efficient blows, making hydraulic hammers indispensable in construction, mining, and excavation.
How a Hydraulic Hammer Works
A hydraulic hammer operates by converting hydraulic energy into high-impact blows, allowing it to break rock, concrete, and other tough materials. It is powered by hydraulic fluid supplied by its carrier—an excavator, backhoe, or skid steer. The hammer is controlled using an auxiliary valve on the carrier. If the carrier lacks this valve, an auxiliary control can be integrated into the hammer itself.
Among hydraulic attachments, hammers require some of the highest hydraulic fluid flow to function properly. The operation cycle consists of four main stages.
1. Upstroke: Lifting the Piston
The cycle begins when the operator presses the hammer tool against a hard surface and activates the hydraulic control valve. This directs oil into the hammer’s inlet, which moves through internal channels until it reaches the main spool valve.
As the oil flows, it pushes the main spool valve downward, allowing hydraulic fluid to enter the lower piston chamber. The increasing pressure forces the piston upward in its bore—this is known as the upstroke.
In nitrogen-assisted hammers, this upward motion also compresses nitrogen in a chamber above the piston, storing energy for the next impact. In hammers like Tramac models (which do not use nitrogen), the upstroke increases hydraulic pressure in an energy chamber, which later assists in the downward motion.
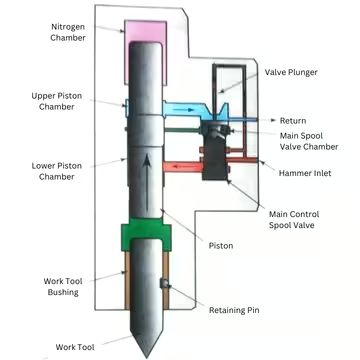
The upstroke begins as hydraulic fluid pushes the piston upward, storing energy for impact.
2. Spool Valve Shift: Preparing for Impact
As the piston moves up, oil in the lower chamber is redirected to the spool valve’s center passage. Since the center of the spool valve has a larger area than the top, it shifts upward, rerouting the oil flow and setting the hammer up for the next phase.
3. Power Stroke: The Downward Impact
With the spool valve shifted, the oil supply to the lower piston chamber is blocked, while hydraulic fluid is redirected to the upper chamber. The compressed nitrogen now forces the piston downward at high speed, delivering a powerful impact.
As the piston moves down, the oil in the lower chamber exits through return passageways, ensuring a smooth stroke. When the piston reaches a certain position, the spool valve’s center passageway opens, releasing pressure and resetting the system.
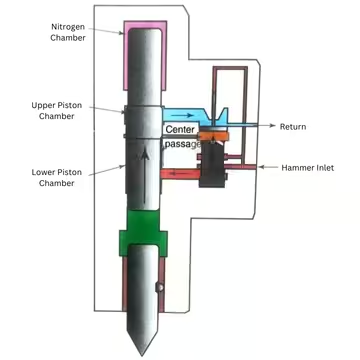
The spool valve shifts, changing oil flow paths to prepare for the downward power stroke.
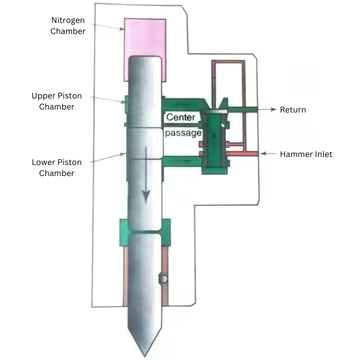
The compressed nitrogen and hydraulic pressure force the piston down, creating high-impact energy.
4. Impact: Breaking the Material
The final stage is the impact, where the piston forcefully strikes the breaker tool. This impact generates a compression wave, which transfers energy through the tool to the rock or concrete at the speed of sound, breaking the material.
Once the piston reaches the bottom of its stroke, the cycle automatically resets, allowing the process to repeat.
Dry-Firing and Its Effects
If the work surface has already been broken but the hammer continues to operate, it enters a condition known as dry-firing. This means the piston is striking without proper resistance, which increases wear and reduces the hammer’s lifespan.
To prevent this, some hydraulic hammers have a dry-fire prevention system, ensuring that the hammer only operates when pressed against a hard surface. Indeco’s rock breakers have this feature built into them.
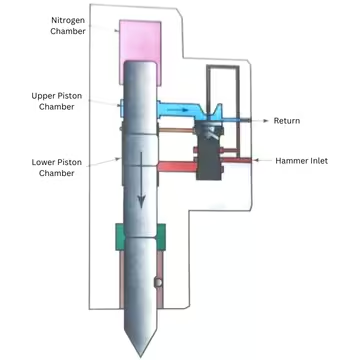
The hammer tool delivers a high-force impact, transferring energy to break the material.
Types of Hydraulic Rock Breakers
Hydraulic rock breakers come in three primary types: Side Type, Top Type, and Silent (Box) Type. Each is designed for specific applications, offering different advantages in terms of performance, durability, and ease of maintenance.
Side Type Rock Breaker
The Side Type Rock Breaker is designed for flexibility and ease of use, making it ideal for applications that require manoeuvrability.
- Shorter overall length: Provides better control and ease of handling.
- Straightforward maintenance: Open design allows for quick part replacements.
- Cost-effective solution: Fewer components reduce maintenance downtime.
Best for: General demolition, trenching, and rock breaking in confined spaces.
Top Type Rock Breaker
For projects demanding higher impact force and greater durability, the Top Type Rock Breaker is the preferred choice.
- Balanced design: Eliminates side weight, reducing chisel breakage.
- Greater impact force: Longer length and heavier mass increase efficiency.
- Ideal for excavation work: Designed for deep penetration and consistent performance.
Best for: Large-scale excavation, foundation work, and breaking through tough rock formations.
Silent (Box) Type Rock Breaker
When noise control is a priority, the Silent Type Rock Breaker provides a quieter yet powerful alternative.
- Enclosed housing: Protects internal components from dust and debris.
- Reduced vibration & noise: Rubber damping minimizes operational noise.
- Extended lifespan: Lower impact stress on components increases durability.
Best for: Urban construction, residential projects, and noise-sensitive environments.
How to Choose the Right Type?
- Side Type: Mounted with installation pins on the side → Quick maintenance & easy handling.
- Top Type: Mounted with installation pins on the top → More impact power & reduced chisel wear.
- Silent Type: Fully enclosed with rubber damping → Lower noise levels & longer lifespan.
If you need raw power, opt for a Top Type breaker. For jobs in urban areas, the Silent Type ensures compliance with noise regulations.
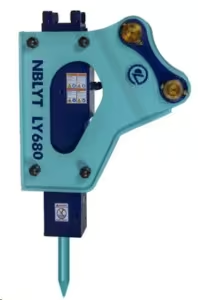
Side Type Rock Breaker
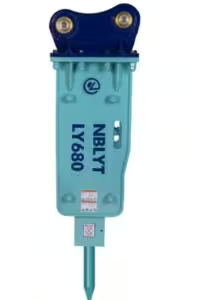
Top Type Rock Breaker
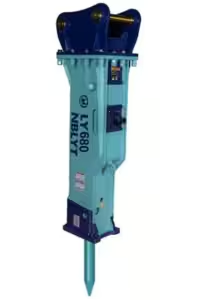
Silent Type Rock Breaker
Calculation of Rock Breaker Impact Energy
Impact energy, measured in joules (J), determines the force needed to break a material. But is maximizing impact energy always the right approach? Let's break it down.
The energy of a single blow from a hydraulic hammer is calculated as:
E = m × (V2 / 2)Where:
- E = Impact energy (Joules)
- m = Striker mass (kg)
- V = Maximum striker velocity (m/s)
Typical striker speeds range between 8–15 m/s, with some heavy-duty breakers exceeding 20 m/s. However, increasing speed beyond safe operating limits can lead to seal wear, excessive heating, and mechanical failure due to increased friction.Choosing the right hammer isn’t just about impact energy—it’s about balancing efficiency, durability, and cost-effectiveness for peak performance.
Advantages and Disadvantage of Hydraulic Hammers
- Adjustable Impact Energy: The impact energy can be precisely adjusted between 10 and 72 kNm, allowing optimal performance across various soil conditions.
- Superior Penetration: With high-impact energy, hydraulic hammers can drive piles into dense and frozen soils without requiring additional techniques like jetting or electroosmosis.
- Continuous Operation: An advanced cooling system enables 24/7 operation without overheating, ensuring maximum efficiency.
- Minimal Pile Damage: The optimised energy transfer prevents damage to pile heads, even under maximum power.
- Reduced Vibrations: A built-in shock-absorbing system minimises ground vibrations, allowing pile driving near existing structures (within 1.5 to 2 meters) without compromising stability.
The primary drawback of hydraulic hammers is their higher cost, often several times that of diesel hammers. However, their long-term efficiency, durability, and performance often outweigh the initial investment.
Common Malfunctions and Causes
Hydraulic hammers can fail due to excessive workloads and insufficient maintenance. The most common issues include:
- Failure to Strike: May result from incorrect connection, improper pressure settings, or insufficient hydraulic oil.
- Irregular Striking Rhythm: Caused by damaged valves or pistons, low nitrogen pressure, or striker damage.
- Reduced Impact Power: Often due to poor-quality oil, clogged filters, control valve failure, loose fasteners, nitrogen leakage, or base machine issues.
- Sudden Loss of Impact Force & Hose Vibration: Often results from diaphragm damage in the accumulator, gas leaks, incorrect tool selection, or tool deformation.
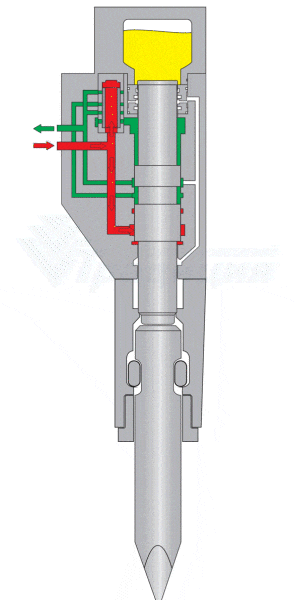
Hydraulic Hammer Working Animation (Source: Tradicia)
If a hydraulic hammer continuously operates without stopping, it may be due to internal oil leaks in the equipment, hydraulic block, or pump system.
Repair and Maintenance
Hydraulic hammers require regular maintenance to ensure longevity and performance.
Hydraulic Fluids: Hydraulic fluid degrades over time due to contamination, overheating, or air bubbles. Regular oil sampling ensures sufficient quality, preventing damage to the hammer and carrier machine.
Hose Couplers: Standard couplers may restrict oil flow and increase operational temperatures. Some hammers, like NPK hammers, require manufacturer NPK specific couplers.
Nitrogen Gas: Nitrogen leaks over time, weakening hammer performance. If frequent recharging is needed, seals may require replacement. Always release nitrogen before disassembly for safety.
Frequently Asked Questions
- What factors affect hydraulic hammer power?
Three key factors influence impact power:
- Nitrogen pressure – Overcharging prevents hammering, while low pressure weakens impacts.
- Hydraulic flow – Excessive flow can cause hammer damage.
- Impact rate – Slower impacts deliver stronger blows, while higher frequency results in lighter impacts.
- How often should the seal kit be replaced?
Every three months, depending on usage and working conditions.
- Can a broken piston be repaired?
No, damaged pistons must be replaced immediately to prevent further damage.
- What causes piston damage?
- Contaminated oil
- Worn inner bushings
- Lack of lubrication
- Can a hydraulic breaker cylinder be repaired?
Minor scratches can be polished once, but further polishing compromises durability.
- Why does the hydraulic hammer suddenly stop working?
- High backhead pressure – Reduce nitrogen pressure.
- Oil leakage into the backhead – Requires seal replacement.
- Stuck control valve – Clean or replace the valve.
- Insufficient oil flow – Repair the pump or adjust the hammer valve.
- Why is the impact force weak?
- Low back pressure
- Contaminated hydraulic oil
- Low operating pressure
- High return line pressure
- Incorrect tool engagement
- Why is the hydraulic hammer not working after installation?
- Improper bushing replacement
- Incorrectly installed quick couplers
- Reversed supply hoses
- High nitrogen pressure
- Closed stop valve
- Why is blank firing harmful?
Blank firing (striking without contacting a surface) causes severe internal damage, leading to:
- Cracked pins and bolts
- Broken front head
- Premature wear of hammer components
Avoid blank firing to prevent costly repairs and extend the hammer’s lifespan.
Research
A Novel Predictable Rock Breaker Using Intelligent Hydraulic Control with ICT Convergences
Conclusion
Hydraulic rock breakers are a key piece of equipment in excavation, demolition, and construction. Their power, precision, and efficiency make them essential for breaking through tough materials like rock and concrete. Choosing the right breaker for the job helps improve productivity and reduces wear on equipment. Like any heavy machinery, hydraulic hammers require regular maintenance to perform at their best. While they cost more upfront than diesel hammers, they often last longer and have lower operating costs, making them a smart long-term investment. By understanding how they work, selecting the right type, and following proper maintenance practices, you can prevent breakdowns, extend their lifespan, and ensure smooth operation. A well-maintained breaker saves time, money, and effort—keeping projects on track and minimising downtime.
If you enjoyed this post, I’d really appreciate it if you could subscribe. I’m 100% planning to dive deep into hydraulics and break it down into simple terms for you!